Склады компании «Русский холод» продолжают переход под управление EME.WMS. Очередной этап масштабного проекта
НАЗАДВ результате внедрения EME.WMS складские процессы «Русский холод» выстроены согласно производственному плану, осуществлен контроль сроков годности продуктов, повышена эффективность логистических операций.
Концерн «Русский холод» - один из ведущих производителей мороженого не только в Москве, но и по всей России. Концерн имеет 14 филиалов в крупнейших городах России и странах ближнего зарубежья, собственные фабрики мороженого в гг. Москва и Барнаул. Заводы оснащены самым современным оборудованием, которое позволяет производить более 150 видов мороженого. Подтверждением высочайшего качества мороженого является получение «Русским Холодом» Европейского регистрационного номера № 1 и права продавать продукцию в США.
Концерн постоянно развивает и совершенствует производственные и бизнес-процессы, в т.ч. по управлению логистическими цепочками. В 2023 г. руководством «Русский холод» было принято решение об автоматизации складов компании и внедрении системы WMS. В результате тендера была выбрана EME.WMS.
Проект был начат с автоматизации региональных комплексов. Первым под управление EME.WMS перешел склад в г. Екатеринбург площадью 1300 кв. м, состоящий из 9 отдельных помещений на одной площадке.
В результате внедрения были автоматизированы основные складские процессы, организована работа с маркированным товаром, обеспечен контроль сроков годности.
Вторым этапом проекта стала оптимизация работы складов в г. Краснодар общей площадью 2660 кв. м. с объемом хранимого товара – 1600 паллетомест.
В результате проекта были запущены теплый и холодный склады, на которых хранятся товары глубокой заморозки и бакалея. Учтены особенности отгрузки по зонам доставки и работы с весовым товаром, а также процессы, связанные с одновременной работой большого количества сотрудников.
EME.WMS отлично зарекомендовала себя при работе на региональных складах. Третьим этапом проекта стала автоматизация основного склада «Русский холод» в г. Москва.
На складе площадью 3000 кв.м. хранятся продукты питания, полуфабрикаты глубокой заморозки. Общее количество SKU – 1500 шт. Товары размещены в 2700 ячейках, около 50% которых – набивные ячейки на 5 паллет. Остальные 50% представлены набивными стеллажами.
Помимо автоматизации основных складских процессов в ходе проекта необходимо было осуществить контроль сроков годности, уйти от зависимости от «человеческого фактора», подготовить склад к переходу на работу с маркированным товаром.
Перед внедрением EME.WMS необходимо было решить ряд сложных задач, связанных с производственными бизнес-процессами. Проблема заключалась в отсутствии у производства четкого плана по объему выпускаемой продукции, заведенного в ERP. Вся информация хранилась в Excel-таблицах. Поэтому для последующей передачи данных в EME.WMS необходимо было прежде всего организовать перевод информации в ERP.
Внедрение EME.WMS позволило осуществлять приёмку продукции из производства до 6 раз в сутки по единому плану производства.
Далее, исходя из производственного плана, система производит просчёт оптимального размещения товара – либо в набивные стеллажи, либо для дальнейшей отгрузки на склады ответственного хранения.
При приемке сразу организован анализ ASN и просчет размещения - после формирования паллеты на SSCC печатается еще и адрес хранения, что позволяет кладовщикам, которые развозят паллеты в зоны размещения, работать без использования ТСД. Сам приказ на размещения выполняет сотрудник на штабелере с использованием ТСД.
Также системой анализируется вес паллеты. В набивные стеллажи на верхние уровни просчитываются для размещения более легких паллет, в нижние уровни – тяжелых паллет.
Важной особенности проекта стала реализация контроля экспортного товара по стране-получателю на всех этапах хранения и отгрузки, инвентаризации. Товары для разных стран имеют различную маркировку. Благодаря внедрённой технологии ошибка при подборе теперь исключена.
Для повышения производительности при обработке возвратов EME.WMS позволила осуществлять возврат по консолидированным заказам с помощью одного сканирования ТСД.
В результате проекта автоматизированы все складские процессы. Осуществлен полный контроль сроков годности товаров. Зависимость от «человеческого фактора» снизилась до «0». Склад активно готовится к работе с маркированным товаром.
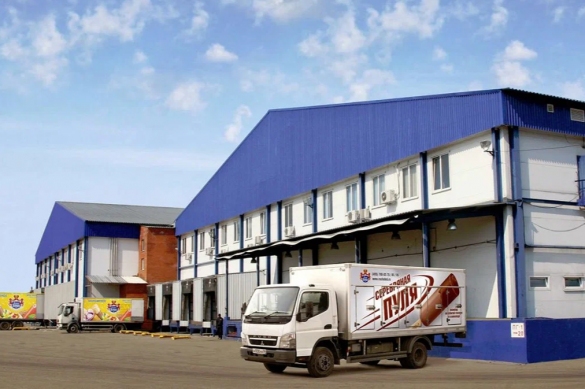